Table of Contents
ToggleIntroduction
In the realm of business and organizational development, continuous improvement is the guiding light that illuminates the path to sustained growth. Amidst an ever-evolving marketplace, companies must adopt a proactive stance, consistently seeking to optimize their processes, products, and services. This article delves into the various strategies businesses can employ to promote continuous improvement and ensure consistent growth, traversing topics such as incremental advancements, radical innovation, and the importance of fostering a culture of constant learning.
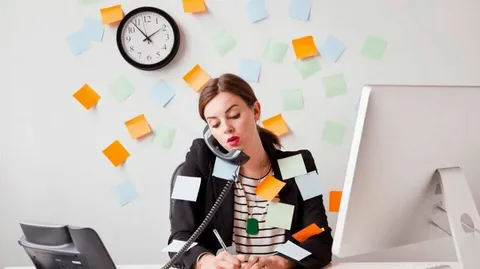
Continuous Improvement
Continuous improvement, also known as Kaizen, is an ongoing effort to enhance products, services, or processes. These efforts can seek “incremental” improvement over time or “breakthrough” improvement all at once.
Historical Perspective
The philosophy of improvement has its roots in the post-World War II Japanese management concept of “Kaizen.” Seeking to rebuild their economy, Japanese industries adopted a strategy of small, constant, positive changes, eventually leading to major advancements and global competitiveness.
Key Principles
There are several key principles underlying continuous improvement. Among these are the importance of employee empowerment, a culture of open communication, a focus on customer needs and expectations, a commitment to data-driven decision-making, and an understanding that improvement is a continuous, not a one-time, effort.
Role of Innovation
Innovation plays a critical role in improvement. Without the willingness to experiment with new ideas and approaches, incremental improvements can become stagnant, and breakthrough improvements may never occur. Therefore, fostering a culture of innovation is essential to the continuous improvement process.
Pillars of Continuous Improvement
Lean Methodology
Lean Methodology is another essential strategy in the improvement arsenal. Originating from Toyota’s production system, the Lean approach focuses on reducing waste and inefficiencies in operations while maximizing productivity. It emphasizes streamlining processes, improving flow, and delivering value to the customer efficiently.
Principles of Lean Interact
The principles of Lean interact synergistically to drive optimal results. For example, ‘Just in Time’ production reduces inventory costs and waste, while ‘Jidoka’ (autonomation) helps identify and correct problems in real-time. When used together, these principles create a cycle of improvement where efficiencies are continually identified and enhanced.
Six Sigma
Six Sigma, another key facet of continuous improvement, is a data-driven approach that seeks to eliminate defects and reduce variability in processes. The main objective of Six Sigma is to enhance the quality of output by identifying and removing the causes of defects and minimizing variability in manufacturing and business processes.
Integrating Six Sigma
Integrating Six Sigma with other improvement strategies can yield substantial benefits. For instance, when combined with Lean methodology, it can lead to Lean Six Sigma, a powerful tool that not only reduces waste and promotes efficiency but also improves quality by reducing variability. The integration of these strategies allows organizations to reap the benefits of both, resulting in a robust continuous improvement framework.
Adapting Methodologies for Continuous Improvement
Agile Methodologies, initially conceived for software development, can be effectively adapted for improvement in various business contexts. Agile is characterized by its emphasis on flexibility, collaboration, and customer satisfaction. In the realm of continuous improvement, Agile practices promote regular reflection and adaptation of processes to optimize efficiency and quality.
By employing iterative work sequences known as sprints, teams can focus on manageable chunks of work, allowing for rapid response to change and continuous improvement. Furthermore, Agile’s principle of cross-functional team collaboration fosters a culture of shared responsibility for improvement, encouraging every team member to contribute ideas and solutions. As such, Agile Methodologies, when properly adapted, can significantly accelerate the pace of continuous improvement in an organization.
Human Element
In the quest for improvement, the human element plays a pivotal role. Leadership, in particular, has a significant impact on shaping and nurturing a culture that fosters continuous improvement. Leaders create the vision, set the tone and expectations, and guide their teams toward the realization of continuous improvement goals.
Impact of Leadership Styles
Leadership styles can dramatically influence the effectiveness of continuous improvement initiatives. Transformational leaders, who inspire and motivate their teams towards a common vision, can effectively foster a culture of continuous improvement. On the other hand, transactional leaders who focus primarily on tasks and performance can also drive improvement by setting clear expectations and rewarding achievement.
Employee Empowerment and Its Link to Success
Employee empowerment is a vital component in the pursuit of continuous improvement. Empowerment refers to giving employees the authority and autonomy to make decisions about their work, fostering a sense of ownership and accountability. When employees feel empowered, they are more likely to take initiative, find creative solutions, and contribute more effectively to improvement efforts. Moreover, empowerment tends to enhance job satisfaction, which in turn, leads to increased productivity and reduced employee turnover. In essence, employee empowerment and satisfaction play a pivotal role in the success of an organization’s continuous improvement strategy.
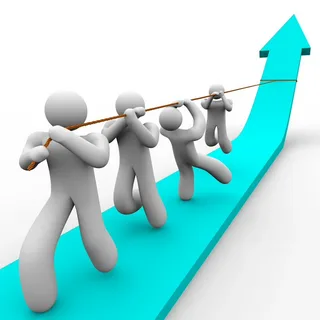
Overcoming Challenges in Continuous Improvement
Continuous improvement is a journey fraught with challenges that can impede progress. However, these obstacles can be overcome with strategic foresight and planning. One of the prominent challenges is resistance to change. Employees may resist new methodologies due to fear of the unknown or comfort with current practices. This can be mitigated through transparent communication, adequate training, and creating a safe environment for employees to voice concerns.
Another challenge may arise in the form of a lack of clear direction or objective. Setting clear, measurable goals that align with the organization’s mission and vision can help to maintain focus and provide a roadmap for improvement. Lastly, improvement efforts may be hindered by an overreliance on data and neglect of the human aspect. Balancing data-driven strategies with attention to employee well-being and involvement can foster a culture of continuous improvement that is both effective and sustainable.
FAQs
What is the key objective of continuous improvement?
The key objective of continuous improvement is to consistently enhance operational processes, reduce waste, and augment the quality of output in business and manufacturing processes.
Can lean and Six Sigma methodologies be integrated?
Yes, Lean and Six Sigma methodologies can be integrated to form Lean Six Sigma. This approach combines the waste-reducing principles of Lean with the defect-reducing techniques of Six Sigma, enhancing efficiency and improving quality.
How can agile methodologies contribute to continuous improvement?
Agile methodologies emphasize flexibility, collaboration, and customer satisfaction. By promoting regular reflection and adaptation of processes, Agile methodologies can significantly accelerate the pace of continuous improvement in an organization.
Conclusion
Continuous improvement is not just a concept, but a culture that organizations need to adopt for sustainable growth and success. By integrating methodologies like Six Sigma and Lean, organizations can effectively reduce waste, enhance efficiency, and improve the quality of their output. The adaptation of Agile Methodologies further accelerates continuous improvement by promoting flexibility and fostering collaboration. However, the success of these strategies largely hinges on the human element. Leadership styles and employee empowerment play pivotal roles in shaping a culture that values and fosters continuous improvement. While challenges are inevitable in this journey, with strategic planning and foresight, organizations can overcome these hurdles and thrive in their pursuit of continuous growth and improvement.